
Temperature regulation
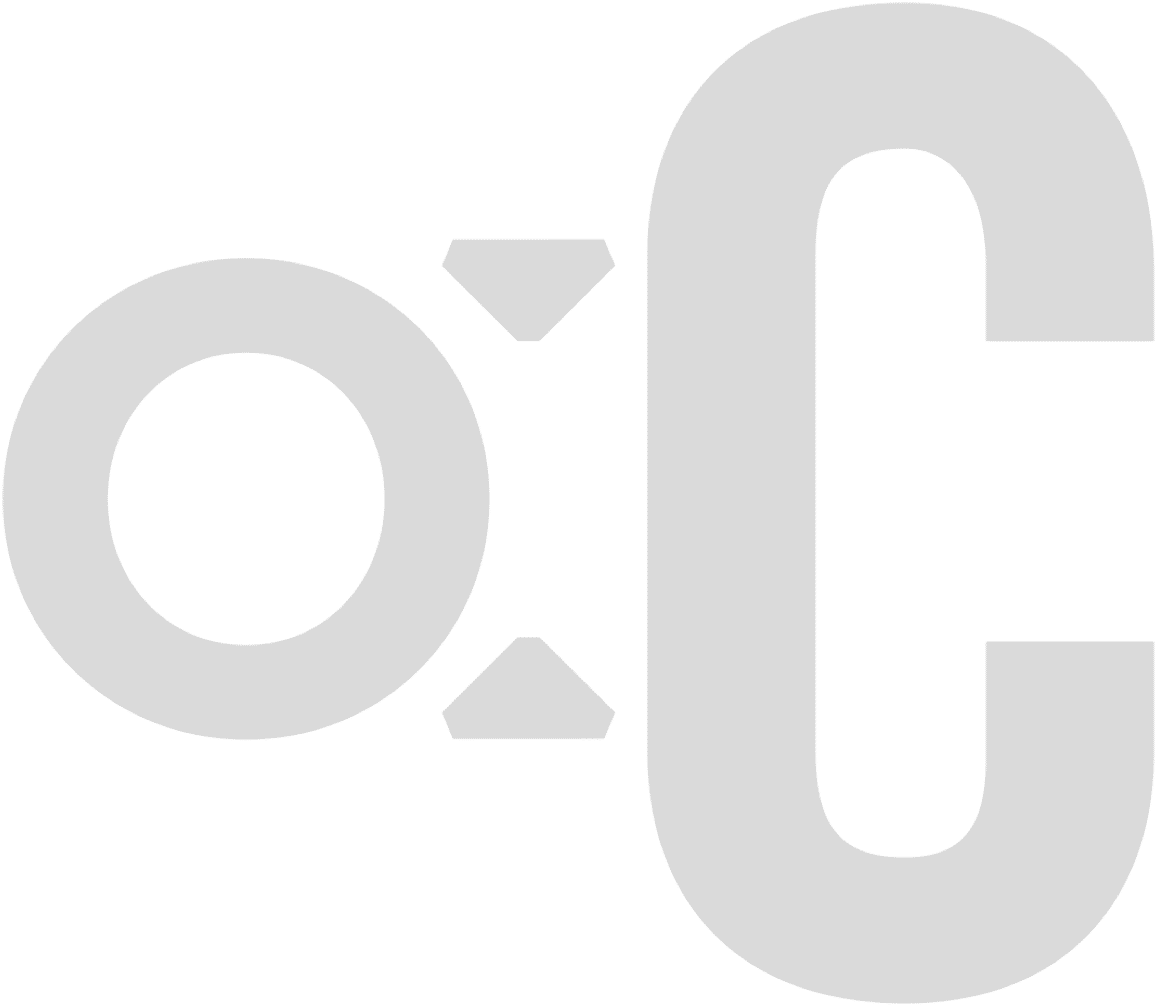
Process-related issues
The temperature of the mass of the reaction medium is an essential parameter to pilot the chemical synthesis process. The Energy Control Unit (or “monofluid” group or thermal skid) is the device for controlling the reaction temperature with the greatest precision and complete safety
The reactor is defined by:
- A capacity with a range between 5 and 40,000 litres depending on the production demand.
- A corrosion resisting material against used reactive products, and even against newborn molecules from the reactions.
- A pressure program with a range between vacuum and 6 bar, but which may go up to 25, 30 bar or even more in case of hydrogenizing processes.
- A temperature program usually located between –20 and +150°c, sometimes at lower temperatures for cryogenically adapted reactors, sometimes at higher temperatures for the distillation of heavier products.
The reactor is sometimes constructed and installed, in order to produce a specific molecule according to a defined reaction path.
However the reactor is often polyvalent to produce various molecules depending on pathways inside pressure and temperature ranges of the device.
The process molecules are tempered and the temperature is regulated by fluid circulation in the jacket of the reactor.
One used regulation technology is direct injection of a disposable fluid in the jacket and the other one is the so-called “monofluid” loop.
The energy skid is the fine chemistry solution to warm up, cool down or control an exothermic reaction.
Le module d’énergies est également utilisé pour réguler la température d’autres appareils que les réacteurs proprement dit : les séchoirs, filtres sécheurs, ”Nutsche” ,… sont également équipés d’une double enveloppe alimentée avec une boucle de fluide thermique ”monofluide”.
The parameter which must be regulated is the reaction temperature. Even if one puts a probe in the reaction, it must not be forgotten that:
TEMPERATURE IS NOT A MEASURABLE PHYSICAL PROPERTY.
Actually, the temperature of a place is evaluated on a scale: 40°c is indeed warmer than 20°c, but one cannot say that the former is twice warmer than the latter.
The Celsius company prefers the use of the Celsius scale, but on occasion, Kelvin or Fahrenheit scales may be used.
The energy skid is made by a thermal fluid loop:
- The thermal fluid works in the whole temperature range in the reactor : it is called “monofluid” because it knows no change between high and low temperature operations.
- The thermal fluid circulates constantly inside the jacket reactor with the help of a regulation pump .
- The thermal fluid receives calories and frigories.
- In some cases the monofluid gets, through exchangers, calories and frigories from steam, water, glycoled water, brine…, even liquid nitrogen. In this case, the energy skid runs in an “close loop” manner.
- Or the monofluid gets calories and frigories by direct injection of warmer or cooler fluid. In that case, the energy skid runs in an “open loop” manner.
- The energy skid can also work in a dual mode in a semi-open loop : this works with heat exchangers for some disposable fluids, in injection mode for some other fluids.
Choice of thermal fluid
The choice of a thermal fluid to transfer calories or frigories to a process depends on temperature and pressure conditions that affect this fluid.
The best thermal fluid is WATER, since it comes with many advantages: very low cost and excellent thermal performance.
However water also has two drawbacks that may prevent from using it:
- Water may be extremely reactive to reactors in the process, which might create an accident in case of containment rupture.
- The specific weight of solid water is lower than this of liquid water. This very rare property of water (only shared with bismuth) is the origin of much damage.
An interesting compromise is this of a thermal fluid based on water:
- BRINE, calcium chloride solution in water, whom fusion point, at a negative temperature, depends on concentration. The thermal performances of brine are higher than those of water, but corrosion from brine limits its use to low temperatures.
- GLYCOLED WATER, a mix of water and glycol ethylene, may be used at low or high temperatures. The addition of glycol brings the advantages of being able to lower the fusion point of water and to reduce saturated steam pressure at high temperatures.
Organic solvents may also be used, pure or with added water, but only at low temperatures to avoid any flaming hazard:
- Ethanoled water, mix of water and ethanol for cold supply network
- Methanol in pure form, for monofluid loop applications in cryogenic mode between –80 and 50°C.
For very low or very high temperatures, or for a working point oscillating between those extreme temperatures, it is necessary to use specific thermal oil.
The use of those oils should be limited to very necessary cases, since they are very expensive but also very flammable.
In France, the use of a thermal fluid at a temperature higher than its flashpoint is ruled by classified installations rules, note #2951.
Each energy skid is shaped and built in a specific manner:
- For a reactor capacity range between a few litres and several dozen cubic meters. This made of stainless steel, hastelloy or glass lined steel, with a jacket, agitated in variable speed by one or more impellers.
- For a temperature program which is defined for mixing, dissolving, distillation, crystallisation, drying and condensing operations.
- For an industrial site with a network of cooling and heating distribution system.
The energy skid is shaped after number of calculations including:
- A hydraulic engineering to calculate the monofluid loop’s flow rate at every temperature. The functioning set point of the pump varies with the temperature according to the specific curve: at a high temperature, the fluid’s viscosity is lower, the pressure drop in the loop and the jacket is reduced and the flow rate is higher.
- A thermal engineering including variants such as the fluid’s speed in the jacket and in the heat exchanger, the wall’s thickness, the speed and the power of agitator, the physical characteristics of the solvents, the exothermal character of the reaction, etc.
- The calculation of Reynolds and Nusselt numbers and exchange ratio in the heat exchanger and between the reactor and the jacket.
- The solving of a system of differential equations leads to the simulation of the mass temperatures’ evolution in the reaction environment and inside the jacket.
The energy skid is controlled by an automatic system letting the operators concentrating on the chemical side of the reaction instead of having to worry about the pure technical aspects of it.
The automatic system is either provided by CELSIUS or centralized by the customer with the reactor’s other functions according to CELSIUS functional analysis.
The main regulation modes are as following:
- Mass temperature regulation in cascade mode according to the jacket’s temperature.
- Jacket’s temperature regulation.
- Limitation of the difference between those two temperatures.
- Transmitted power regulation.
- Reactive product flow rate regulation.
- Heating or cooling scale.
For the energy skids that regulate a reaction, crystallisation or drying temperature – in a dryer, dryer-filter or ‘Nutsche’ -, it is very difficult to measure the product temperature. For those devices, the regulation mode is similar to this of a thermal fluid temperature in the jacket, with a fixed set point or according to a scale.
The energy module is controlled by an automatic system that frees operators from the technical function to focus their attention on the chemistry of the reaction.
The automation is either:
- centralized by the user with the other functions of the reactor but based on the functional analysis of CELSIUS.
- taylor-made by CELSIUS from the functional analysis of CELSIUS with automation equipment chosen by the user
- be supplied by CELSIUS. The Energy Control Unit is then equipped with a CELSIUS automaton with a touch screen, possibly for ATEX zone, and loaded with a standardized and proven program.
The CELSIUS PLC
CELSIUS has developed a PLC and automation programs dedicated to the temperature regulation of synthesis reactors.
The advantages of this policy are:
- The programs have been standardized and proven over many test days. Programming errors and time wasted on debugging on site are avoided.
- The automatic regulation is supplemented by a process simulation program based on the thermal balances established during the design of the unit. Thus, before the delivery of the Energy Control Unit, its operation is simulated for several weeks. At any time, the mass and loop temperatures are calculated according to the position of the valves. These tests optimize the proportional and integral parameters of each regulator. The Energy Control Unit is then delivered with a preset automation depending on the reactor and its operating conditions. Commissioning takes place in less than a day.
- The Energy Control Unit is piloted from a touch screen (ATEX or not) on the operator’s workstation. It can also be controlled remotely from a computer by WEB link.
- CELSIUS controls the hardware and software evolutions of its automata during the many years of future exploitation of the Energy Control Units and without license constraints. Upon request, CELSIUS provides after-sales service for the devices via WEB link.
Fields of application
Temperature regulation of a multi-purpose reactor from -20 to + 150 ° C
Temperature regulation of a cryogenic reactor down to -100 ° C
Temperature regulation of a filter drier or dryer
Need an expert ?
Tell us what you need using our contact form
Our references
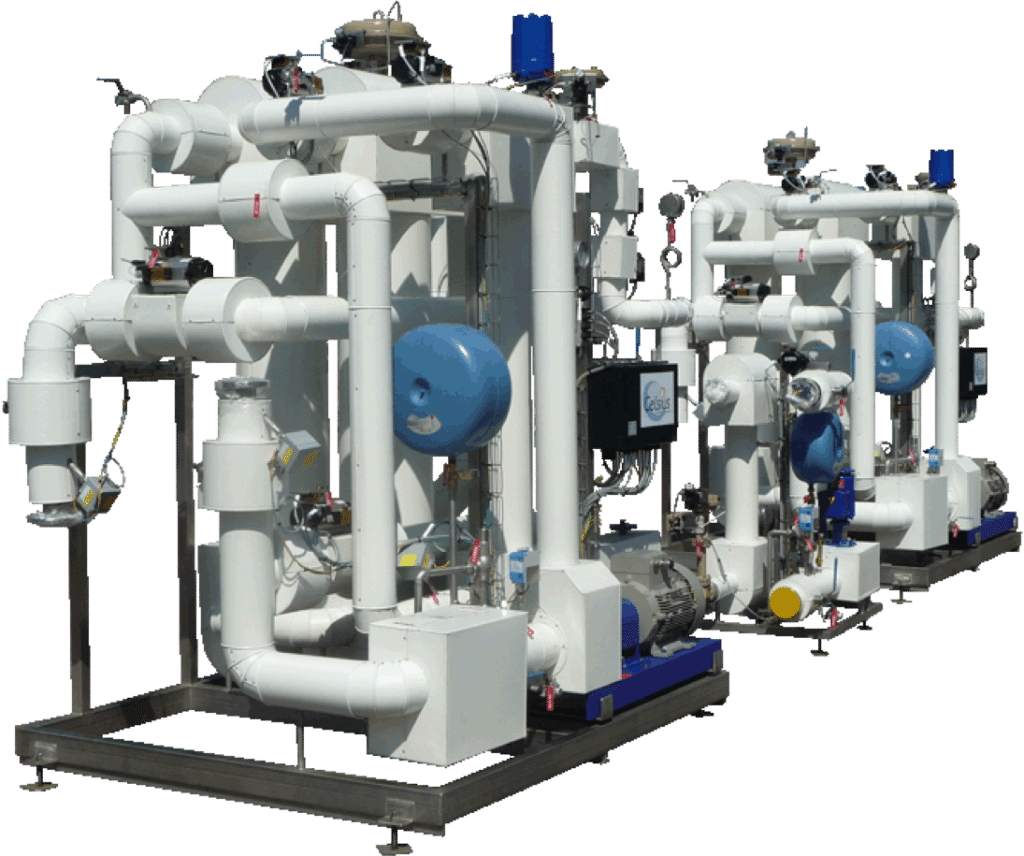
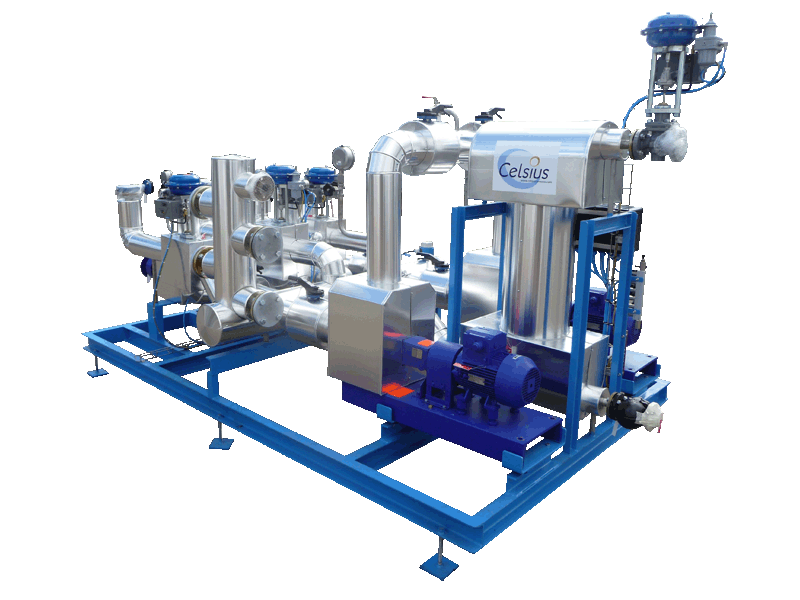
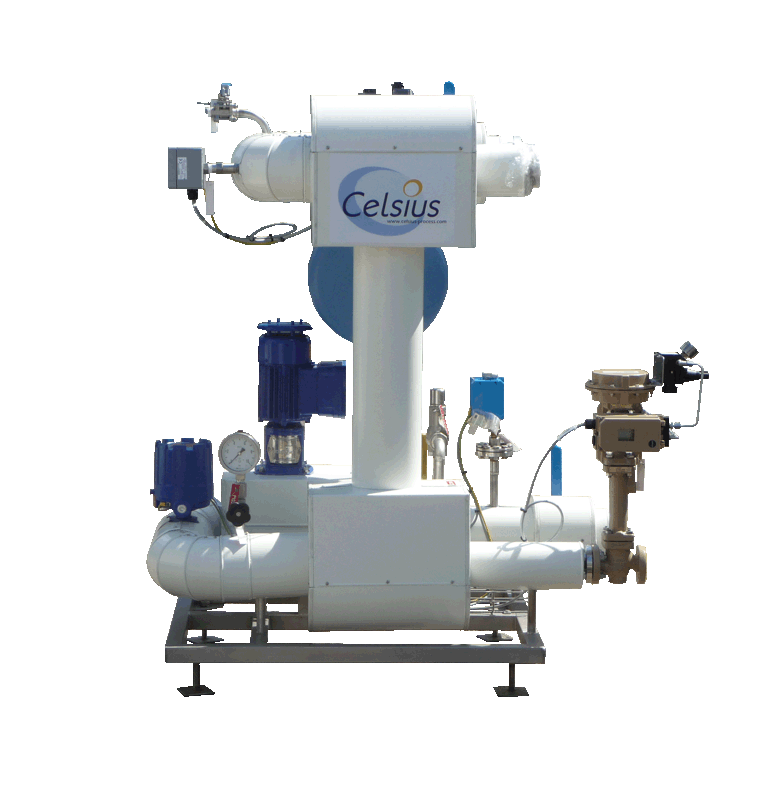

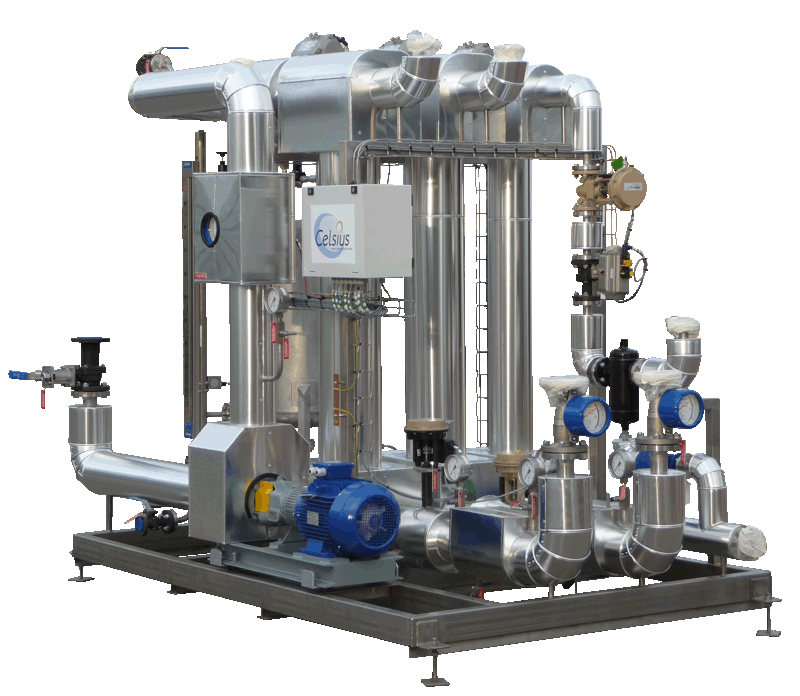
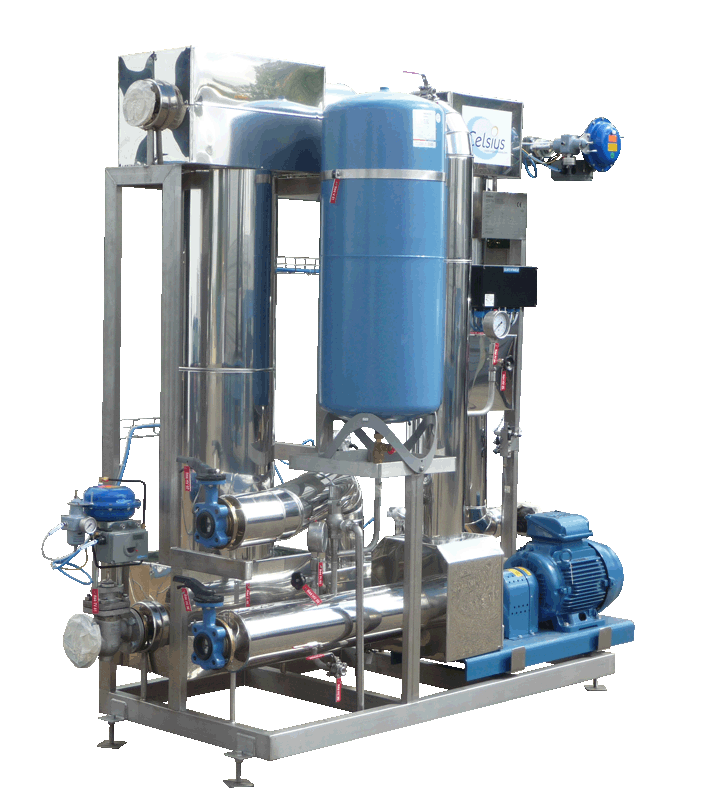
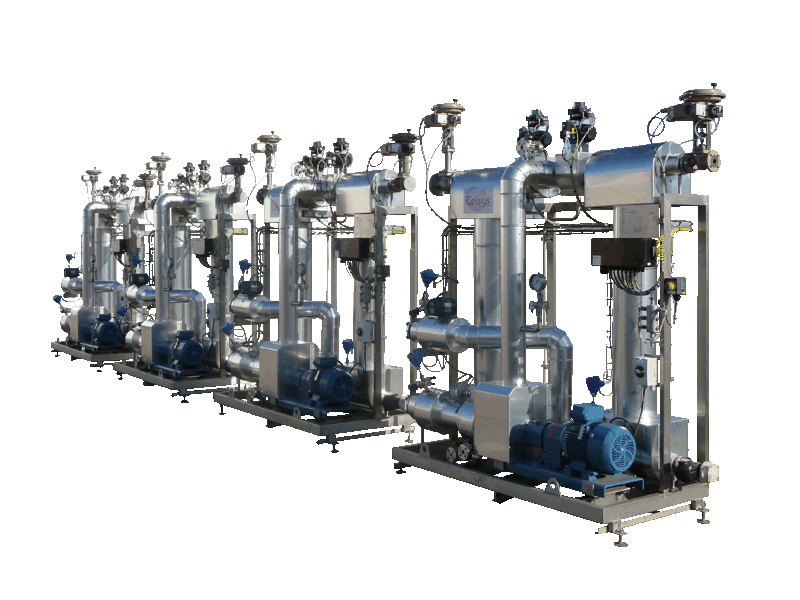
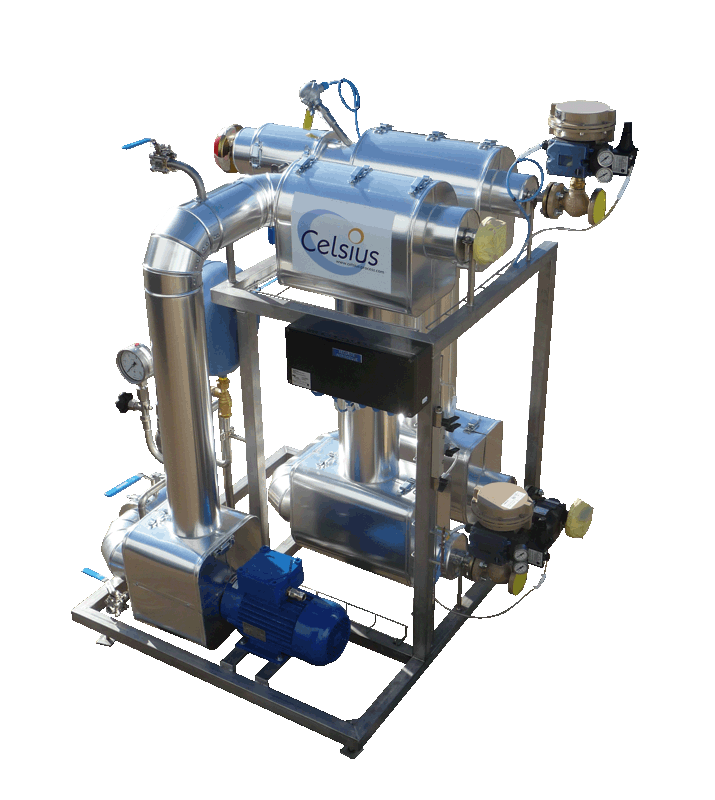
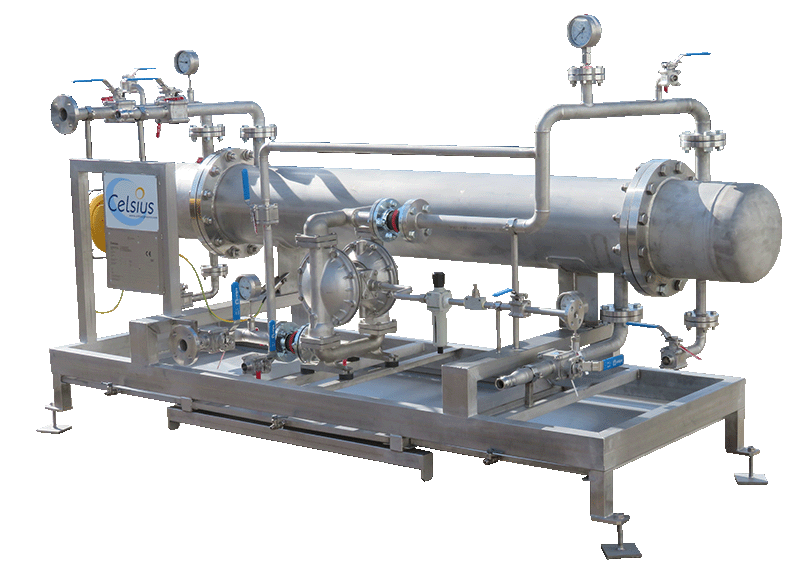
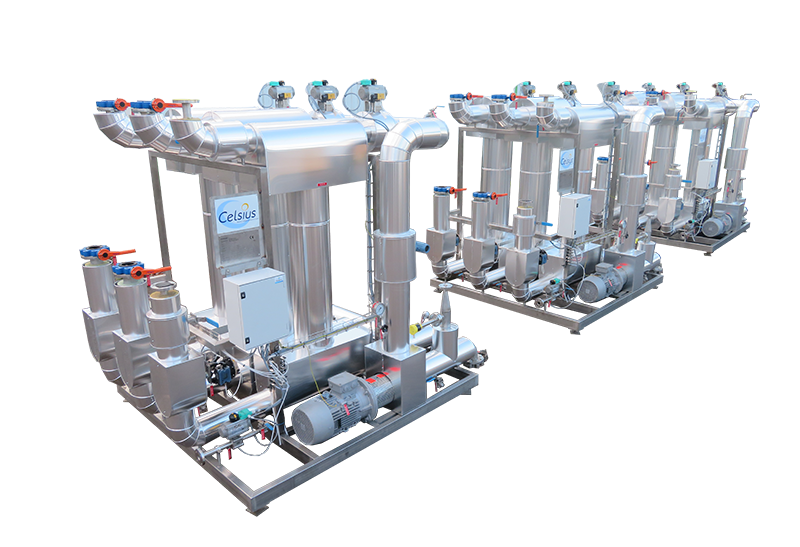
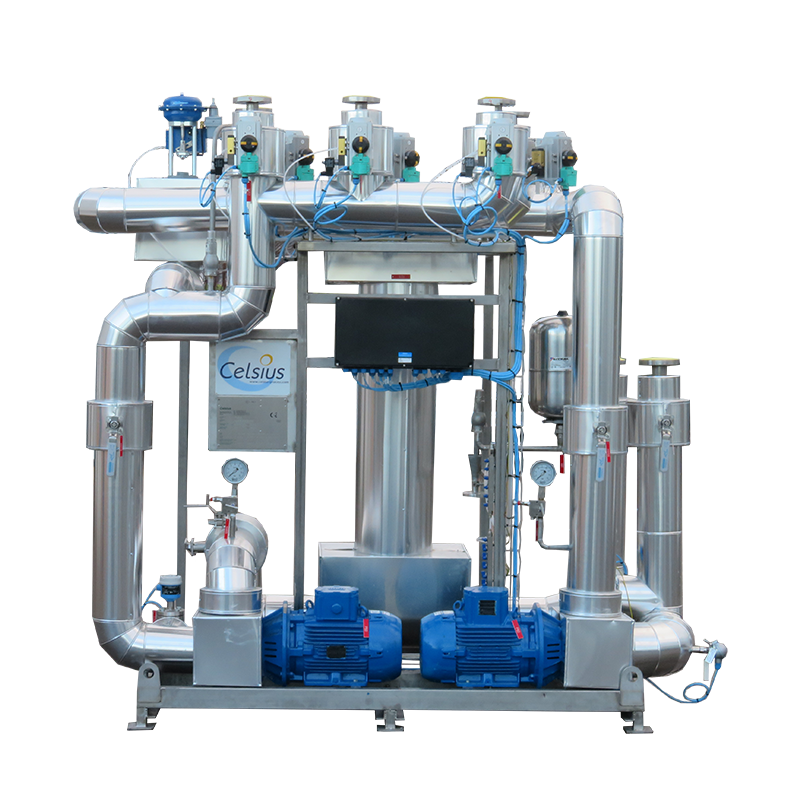
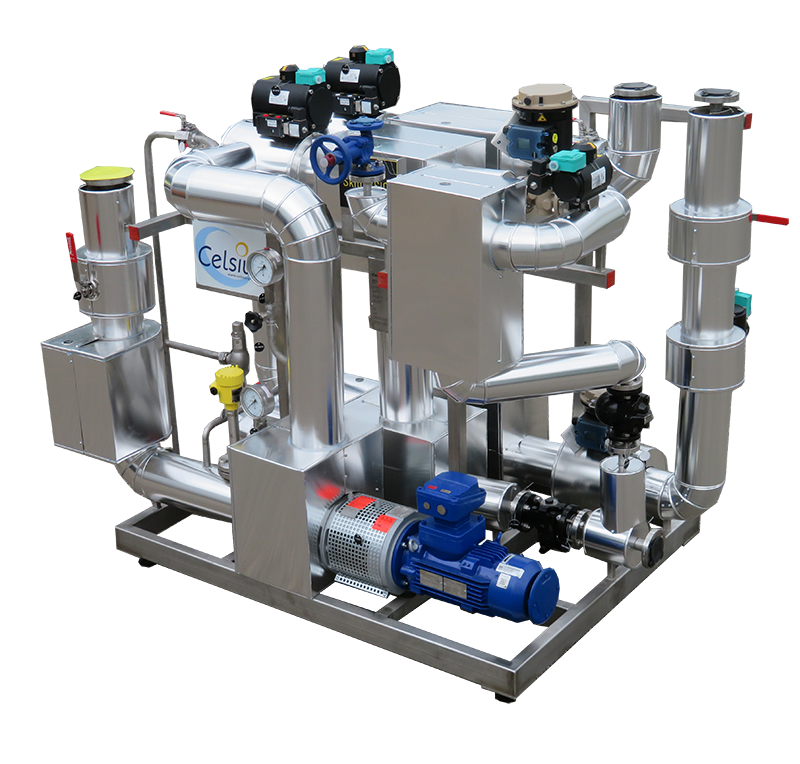
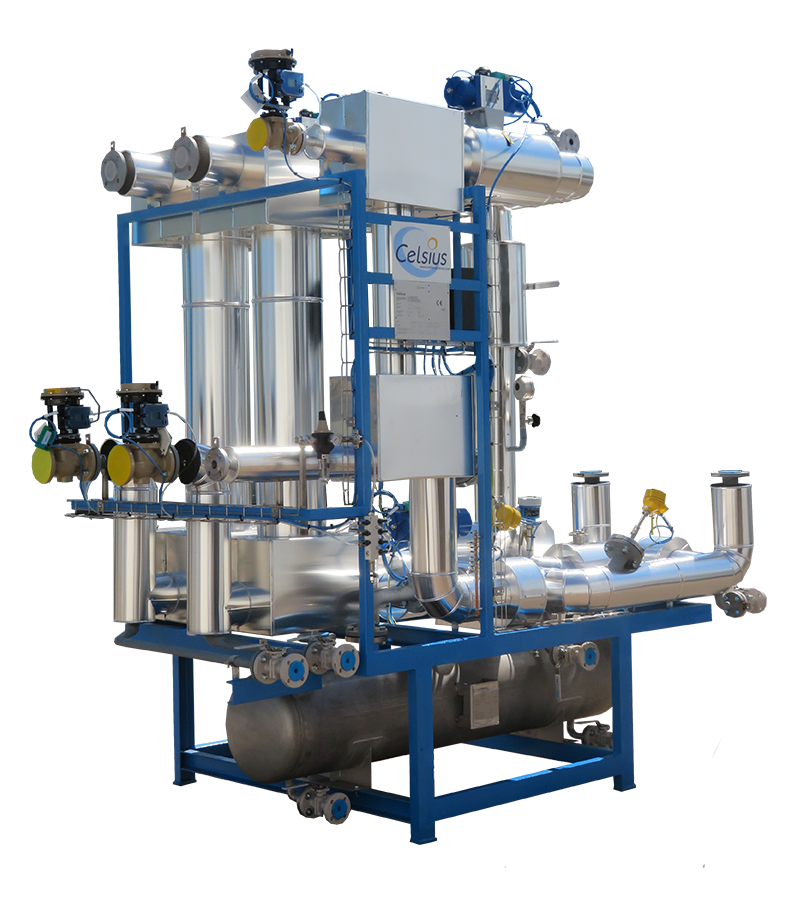
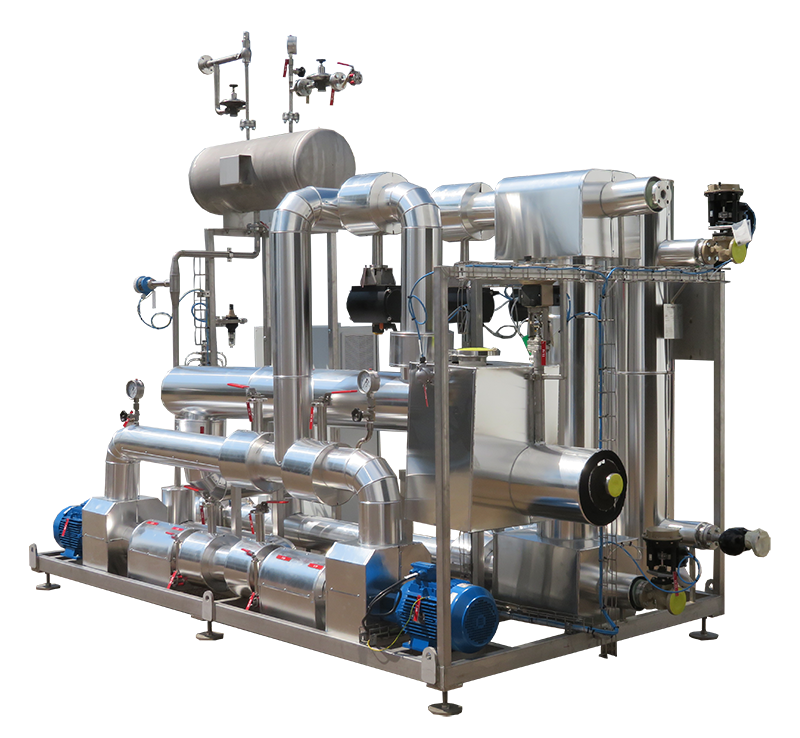
AJINOMOTO EUROLYSINE (Amiens)
1 sterilisation pilot
2007AVENTIS (Vertolaye)
1 Energy Control Unit for 8000 litres reactor
2006BASF PHARMA (Saint-Vulbas)
1 Energy Control Unit for 2500 litres reactor
2012BASF Schweiz (Monthey)
1 Energy Control Unit for 10000 litres reactor
2015BASF Schweiz (Monthey)
1 Energy Control Unit for 100 m3 vessel
2015BENECHIM (Lessines)
1 Energy Control Unit for 2500 litres hydrogenation reactor
2020BERKEM (Gardonne)
2 Energy Control Units for 300 litres reactors
2011BERKEM (Gardonne)
4 Energy Control Units for 300 litres reactors
2012BERKEM (Gardonne)
4 Energy Control Units for 100, 200 and 400 litres reactors
2013CIMO (Monthey)
1 Cooling unit for vessels
2020COOPERL (Lamballe)
Temperature Control Unit for 630 litres reactor
2024ELKEM (Saint Fons)
1 Temperature Control Unit for 1000 litres reactor
2021EURECAT (La Voulte)
1 oil heater
2006EURENCO (Sorgues)
1 Energy Control Unit for 2635 litres reactor
2011EURENCO (Sorgues)
4 Energy Control Units for 3000 litres reactors
2014FINORGA (Chasse sur Rhône)
4 Energy Control Units for 1000 and 4000 litres reactors
2009FINORGA (Chasse sur Rhône)
1 Energy Control Unit for filter dryer
2017FINORGA (Chasse sur Rhône)
1 Temperature Control Unit for filter dryer
2023GREENTECH (Saint Beauzire)
2 Energy Control Units for a reactor and a filter dryer
2013GUERBET (Lanester)
5 Energy Control Units for 4000 and 6300 litres reactors and for condensers
2007GUERBET (Lanester)
1 Energy Control Unit for 4000 litres reactor
2008GUERBET (Lanester)
1 Cooling unit for condensers
2013GUERBET (Lanester)
3 Energy Control Unit for 6300 litres reactors and condensers
2016GUOBANG (Weifang)
1 Energy Control Unit for vessel
2019HENGSHENG (Nanjing)
1 Energy Control Unit for 1000 litres reactor
2019INTEROR (Calais)
3 Temperature Control Units for 6300 to 10000 litres reactors
2023INTEROR (Calais)
3 Temperature Control Units for reactors 4000 litres
2024INTEROR (Calais)
Temperature Control Unit for filter-dryer
2025KEYUAN (Jinan)
14 Energy Control Units for 1000 and 3000 litres reactors
2019LIXIN (Zibo)
1 Energy Control Unit for 3000 litres reactor
2019MINAKEM (Beuvry la Forêt)
1 Energy Control Unit for 4000 litres cryogenic reactor
2010NORCHIM (Saint Leu d'Esserent)
1 Temperature Control Unit for 1000 litres cryogenic reactor
2021PCAS (Limay)
1 Energy Control Unit for 1200 litres reactor
2011PCAS (Couterne)
1 Energy Control Unit for 4000 litres cryogenic reactor
2015PCAS (Aramon)
1 Energy Control Unit for 100 litres reactor
2016PHARMASYNTHESE (Saint Pierre lès Elbeuf)
1 Energy Control Unit for 1600 litres reactor
2012PHARMASYNTHESE (Saint Pierre lès Elbeuf)
2 Energy Control Units for 400 and 3000 litres reactors
2013PHARMASYNTHESE (Saint Pierre lès Elbeuf)
3 Energy Control Units for 100, 400 and 3000 litres reactors
2013PHARMASYNTHESE (Saint Pierre lès Elbeuf)
4 Energy Control Units for 1600 and 4000 litres reactors
2015PPG SIPSY (Avrillé)
1 Energy Control Unit for 1400 litres cryogenic reactor
2007ROQUETTE (Lestrem)
1 Energy Control Unit for 1500 litres reactor
2014SANOFI CHIMIE (Aramon)
1 chiller and 2 Energy Control Units for 150 litres reactor and vessels
2006SANOFI CHIMIE (Aramon)
1 Energy Control Unit for vessels
2007SANOFI CHIMIE (Vertolaye)
1 Energy Control Unit for 4000 litres reactor
2008SANOFI CHIMIE (Aramon)
1 Energy Control Unit for 1000 litres reactor
2008SANOFI CHIMIE (Vertolaye)
1 Cooling Unit for condensers
2014SANOFI CHIMIE (Aramon)
1 Energy Control Unit for high temperature 2000 litres reactor
2019SANOFI WINTHROP INDUSTRIE
Temperature Control Unit for 50 litres reactor
2024SIMAFEX (Marans)
1 Electric heater unit and 11 Energy Control Units for reactors of 250, 1000, 1600 and 2500 litres
2007SIMAFEX (Marans)
3 Energy Control Units for 2500, 6300 and 8000 litres reactors
2010SIMAFEX (Marans)
2 Energy Control Units for 8000 litres reactors
2013SIMAFEX (Marans)
1 Temperature Control Unit for filter dryer
2023Société Suisse des Explosifs (Gamsen)
1 cooling skid for condensers
2013SYNGENTA (Münchwilen)
1 Energy Control Unit for continuous process
2012SYNGENTA (Münchwilen)
2 Energy Control Units for a filter dryer and a condenser
2018TAIPU (Tianjin)
2 Energy Control Units for 500 and 1000 litres reactors
2019TIANDONG (Dongying)
1 Energy Control Unit for 1000 litres reactor
2019WANGBANG (Xuzhou)
8 Energy Control Units for reactors of 150, 200, 1500, 2000 and 3000 litres
2018YILING (ShiJiazHuang)
1 Energy Control Unit for 2000 litres reactor
2020ZACH SYSTEM
1 Energy Control Unit
2009Ressources
It is often difficult to find the physical characteristics necessary for fluids used in chemical engineering calculations. Also, we have grouped this data in a series of tables which you can consult below for the following fluids:
PURE FLUIDS
WATER
Download linkMETHANOL
Download linkETHANOL
Download linkISOPROPANOL
Download linkMETHYLCYCLOHEXANE
Download linkXYLENE
Download linkWATER SOLUTIONS
MEG monoethylene glycol 20%
Download linkMEG monoethylene glycol 25%
Download linkMEG monoethylene glycol 30%
Download linkMEG monoethylene glycol 35%
Download linkMEG monoethylene glycol 40%
Download linkMEG monoethylene glycol 45%
Download linkMEG monoethylene glycol 50%
Download linkMPG monopropylene glycol 25%
Download linkMPG monopropylene glycol 30%
Download linkMPG monopropylene glycol 35%
Download linkMPG monopropylene glycol 40%
Download linkMPG monopropylene glycol 45%
Download linkMPG monopropylene glycol 50%
Download linkETHANOL 10%
Download linkETHANOL 20%
Download linkETHANOL 30%
Download linkETHANOL 40%
Download linkETHANOL 50%
Download linkETHANOL 60%
Download linkETHANOL 70%
Download linkETHANOL 80%
Download linkETHANOL 90%
Download linkMETHANOL 10%
Download linkMETHANOL 20%
Download linkMETHANOL 30%
Download linkMETHANOL 40%
Download linkMETHANOL 50%
Download linkMETHANOL 60%
Download linkMETHANOL 70%
Download linkMETHANOL 80%
Download linkMETHANOL 90%
Download linkSYNTHETIC OILS
Dowtherm J
Download linkDuratherm S
Download linkDynalene MV
Download linkJarytherm AX320
Download linkJarytherm BT06
Download linkJarytherm CF B
Download linkJarytherm DBT
Download linkMarlotherm LH
Download linkMarlotherm SH
Download linkMarlotherm X
Download linkParacryol
Download linkParatherm CR
Download linkParatherm HR
Download linkSantotherm 59
Download linkSantotherm LT
Download linkSyltherm 800
Download linkSyltherm XLT
Download linkTherminol 66
Download linkTherminol ADX10
Download linkTherminol ALD
Download linkTherminol D12
Download linkTherminol XP
Download linkCelsius is also...
Discover one of our key process : Extraction of natural molecules